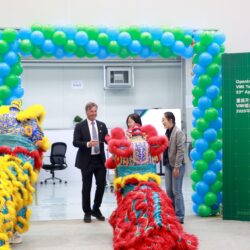
In all of VMI’s industries, technological advances are continuous. But one constant factor is VMI’s total commitment to providing proven, reliable equipment, services and solutions. That is also why VMI created VMI Services: to make sure that you not only operate the best equipment available, but that it also continues to be the best solution.
The VMI Services organization works closely with you to determine your maintenance maturity and requirements. Ranging from regular equipment check-ups with recommendations to complete service packages that include overhauls, upgrades, training or more, our aim is to always optimise the performance of your equipment at predictable costs. Together with our VMI’s advisors, a tailor made VMI maintenance support program can be determined, continuously helping you to improve your process.
Just a phone call away: we are here to help, whether it is for support, modernization or optimalization. For the best solution, always.
For effective plant operation, you need highly skilled and motivated personnel. For this purpose, VMI established the VMI Academy, to enable you to get the best out of your VMI systems. The VMI Academy offers a wide variety of training programs specifically developed for your staff.
Even with the best in class machines and highly educated staff, you will need assistance from time to time. Either to remotely take care of small issues or you may require on-site supervision of major maintenance interventions for example. With VMI’s maintenance services, we are by your side, 24 hours a day, 7 days a week.
Technology never stands still! Developments on technical systems are accelerated by the continuous release of new technologies. As a result of our Research & Development activities, newer and improved functionalities or modules are always being released.
Where should you go for replacement parts? You might be inclined to think the least expensive supplier is the best option. However, buying spare parts at suppliers that do not fully understand the application of the part in the complete machine, may create a risk to your process. VMI continuously re-engineers and improves our parts to reduce Total Cost of Ownership. With VMI original parts, you are guaranteed that the parts fit the first time around.
No-one likes to be burdened with paperwork and reporting, but up to date instant insight in the performance of your equipment allows you to optimally control your processes. That is why VMI has developed various Management Support Tools to make the task of ordering spares, or executing alignment checks as simple as possible. VMI’s management support tools furthermore give you the information you need to make sure your equipment performs up to standard. It also forms the basis of potential improvement projects for process optimization.
The day to day hectic of running production usually prevails and at the same time you have to worry about maintenance slots. Sometimes maintenance is seen as less important and then in the end it brings a lot of stress and consumes a lot of time that was not planned. This could also cause you to lose sight of the long term goals that are needed to achieve your strategic ambitions. VMI fully understands this and has therefore designed our products in a modular way allowing us to combine individual products to complement each other and drive improvements through your organization.